Six Sigma is a method that helps businesses by reducing defects and errors. Using it improves quality and revolutionizes an organization's core capability. It uses a structured approach called the DMAIC process. (Define-Measure-Analyze-Improve-Control)
By implementing it alongside Lean Six Sigma principles, organizations can optimize resources. The article explores how Six Sigma transforms businesses by methodology. It will discuss its benefits and how to use it successfully. Read on below to learn more.
In this article
- Part I: History of Six Sigma
- Part II: Core Principles and Concepts of Six Sigma
- Part III: Useful Diagrams for Six-Sigma Analysis
- Part IV: How To Implement Six Sigma in Organizations
- Part V: Benefits, Challenges, and Limitations of Six Sigma
- Part VI: Six Sigma and Lean Six Sigma – A Comparison
- Conclusion
Part I: History of Six Sigma
Six Sigma was put forward in the late 1980s at Motorola, an American telecommunications company. The method refers to a measure of improving processes by reducing defects and errors in businesses. In essence, a Six Sigma process has a defect rate of less than 3.4 defects per million opportunities.
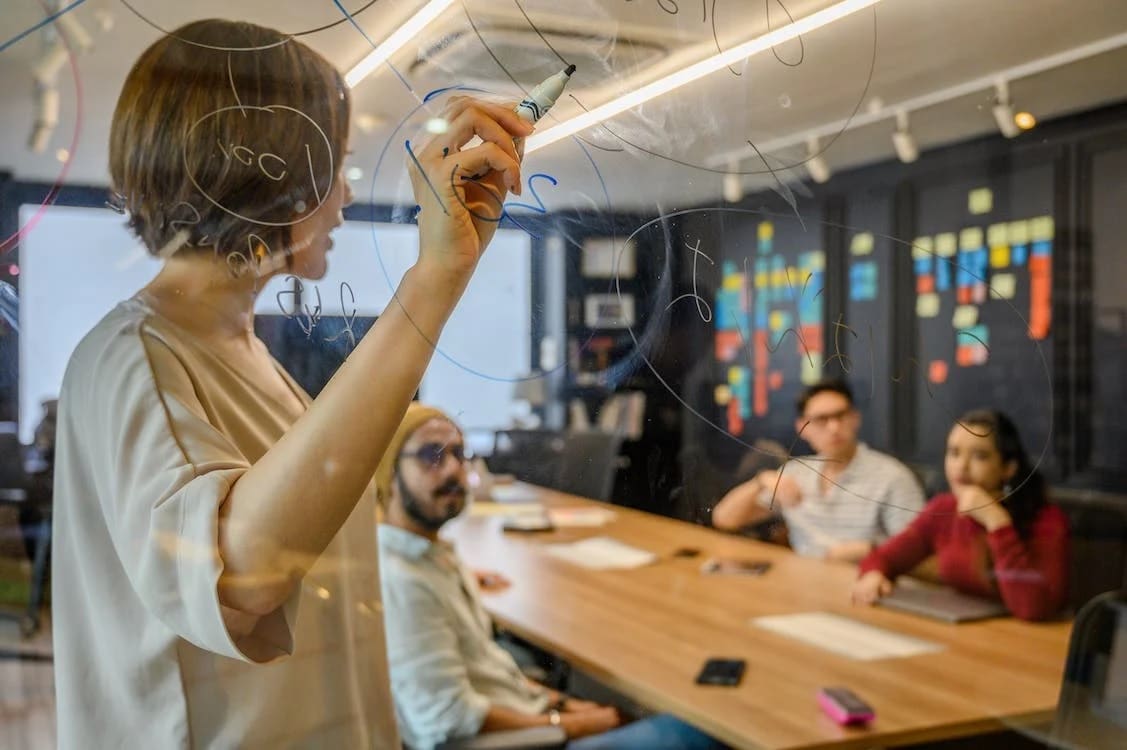
Motorola's Six Sigma program was a success. Other companies, including General Electric, AlliedSignal, and Ford, soon adopted the method. By the early 1990s, Six Sigma was implemented by companies in a wide range of industries. It included manufacturing, healthcare, and financial services.
Key Contributors and Notable Milestones
Some of the key contributors to the development of Six Sigma include:
- Mikel Harry. He is considered the father of Six Sigma for developing many of the tools and techniques used in Six Sigma today.
- Bill Smith. Smith is a Motorola engineer. He was credited with popularizing Six Sigma and making it known to a wider audience. He was also instrumental in developing Motorola's Six Sigma program.
- Jack Welch. Jack Welch served as the CEO of General Electric from 1981 up to 2001. He made Six Sigma a global phenomenon by implementing it at GE and requiring his suppliers to do the same.
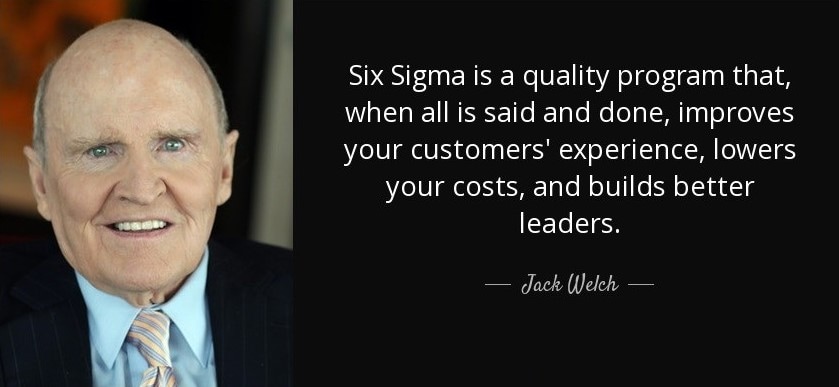
Evolution of Six Sigma Into Different Variations and Approaches
Over the years, Six Sigma has evolved into different variations and approaches.
- Lean Six Sigma. Lean 6 Sigma combines the principles of Six Sigma with the tools and techniques of Lean manufacturing. It is focused on eliminating waste and improving process efficiency.
- Design for Six Sigma (DFSS). DFSS focuses on designing products and processes that are Six Sigma-capable right off the bat.
- DMAIC and DMADV. There are two common methodologies within Six Sigma. DMAIC improves existing processes, while DMADV (Define-Measure-Analyze-Design-Verify) is applied to create new processes or products.
Part II: Core Principles and Concepts of Six Sigma
The section below delves into the core principles of Six Sigma, focusing on the DMAIC methodology's five phases. It will also discuss the distinct roles and responsibilities crucial to successful Six Sigma implementation.
DMAIC Methodology
DMAIC is applied to improve processes within organizations. Here are its five phases.
- Define. This phase sets clear project goals and aligns them with organizational objectives.
- Measure. It quantifies the current process state and identifies areas for improvement.
- Analyze. Data is analyzed to identify the root causes of issues.
- Improve. Solutions are developed and implemented.
- Control. Placing controlled measures to sustain improvements.
Six Sigma Roles and Responsibilities
Six Sigma assigns specific roles and responsibilities to individuals involved in a project:
- Executive Leadership. Provides support, resources, and overall strategic direction.
- Responsible for project selection and aligning Six Sigma efforts with organizational goals.
- Master Black Belts and Black Belts. They lead and execute Six Sigma projects, applying the methodology's tools and techniques.
- Green Belts. Typically support Black Belts in project execution while maintaining their regular job responsibilities.
- Team Members. Collaborate with Belts and provide subject-matter expertise during projects.
- Process Owners. Hold ultimate responsibility for the improved process after project completion.
- Include anyone affected by or interested in the project's outcome, and they may provide valuable input.
Part III: Useful Diagrams for Six-Sigma Analysis
The section below offers diagrams from EdrawMax's Templates Community that can aid you in the process analysis of Six Sigma methodologies. Explore using visual diagrams to enhance your organization's analysis and problem-solving. If you are interested in more such examples, download EdrawMax and explore our templates community.
Six Sigma Concept Map
The concept map highlights Six Sigma and its various aspects. It starts through key concepts like process improvement and variation. It tackles the importance of data-driven decision-making, the benefits of statistical analysis, and potential challenges. The flowchart also addresses industry-specific considerations. It emphasizes the significance of continuous improvement and customer-focused strategies in the Six Sigma methodology.
Six Sigma Matrix Diagram
The matrix diagram below is a visual tool to illustrate connections between different entities within multiple organizations. It assesses the strength of the different relationships. The diagram aids in identifying links, responsibilities, and interest levels among various organizational divisions. It can facilitate effective management and decision-making within the organization.
Six Sigma Process Mapping
The diagram below is a graphical tool for visualizing the sequence of steps in a specific activity or process. Typically presented as flowcharts, it illustrates inputs and outputs step-by-step, aiding process comprehension. Certified Black Belt leaders or team members often craft these maps using specialized software or office tools.
Part IV: How To Implement Six Sigma in Organizations
Implementing Six Sigma involves selecting and scoping projects. Below are the essential elements of a successful Six Sigma initiative.
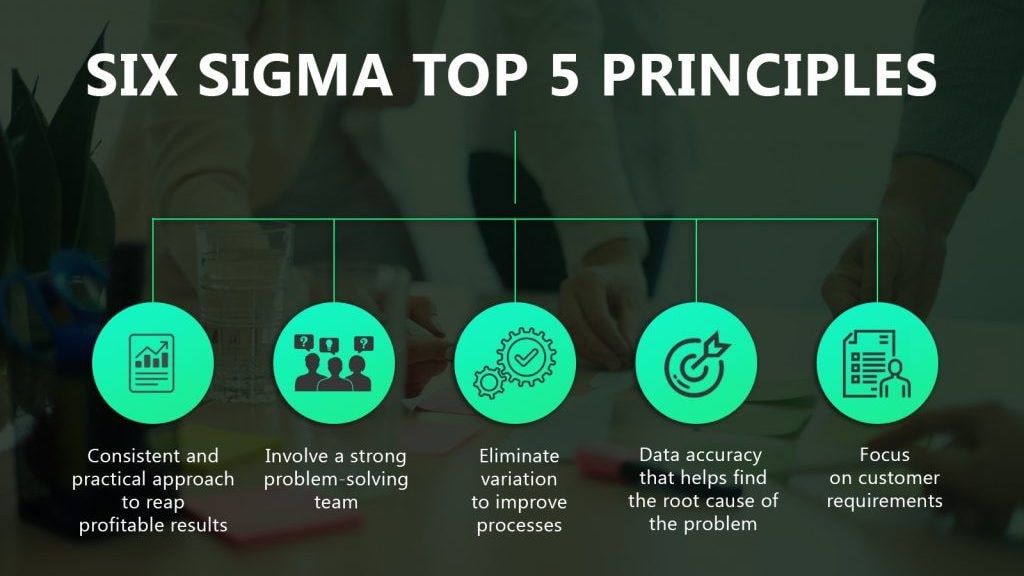
Selecting and Scoping a Six Sigma Project
The first step in implementing Six Sigma is choosing the right project. Organizations should identify critical processes that impact quality, cost, or customer satisfaction. These processes are often identified through customer feedback, historical data, or KPIs. Once a critical process is selected, clear and measurable project goals must be defined. It provides a roadmap for the project team and helps measure the success of the Six Sigma initiative.
Building a Six Sigma Team and Infrastructure
Team members should undergo appropriate Six Sigma training and certification programs, such as Green Belt or Black Belt certification. Next, organizations need a well-defined project management and governance structure. This includes designating project leaders, forming cross-functional teams, and defining roles and responsibilities.
Applying Six Sigma Tools and Techniques
Data is the foundation of Six Sigma. Statistical tools like histograms, control charts, and regression analysis are commonly used to analyze data and make data-driven decisions. Once root causes are identified, improvement strategies are developed and implemented to eliminate or mitigate them. The process may involve process redesign, introducing new technologies, or changes in work procedures.
Part V: Benefits, Challenges, and Limitations of Six Sigma
Six Sigma helps organizations produce more consistent and reliable outcomes. Here are a couple of reasons.
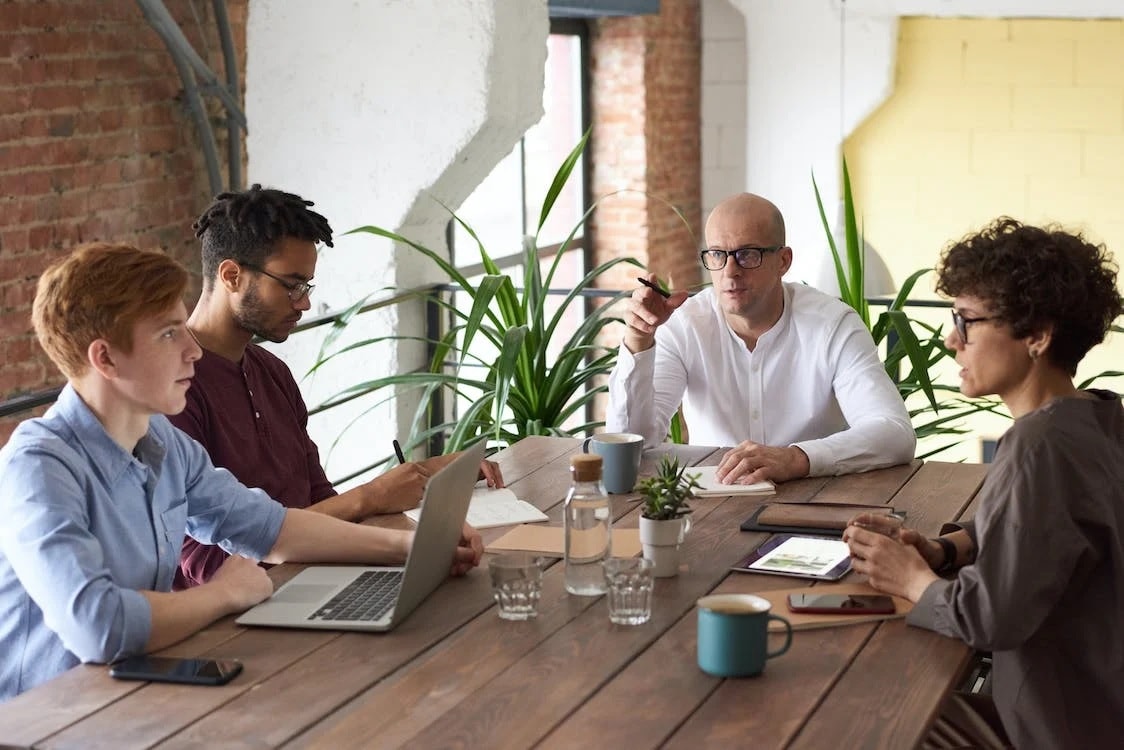
- Improved Quality and Customer Satisfaction
Implementing Six Sigma leads to higher customer satisfaction as customers experience fewer issues with products or services. It can lead to increased quality of products and ensure brand loyalty.
- Cost Reduction and Increase Efficiency
Six Sigma is a potent tool for cost reduction and operational efficiency. Implementing it allows organizations to reduce rework, scrap, and other non-value-added activities. It ultimately saves businesses money.
Successful Examples of Six Sigma Implementations
These real-world examples highlight how Six Sigma can deliver tangible benefits.
- Ford Motor Company. Ford applied Six Sigma principles to reduce defects and enhance vehicle quality. It contributed to its resurgence in the early 2000s.
- Honeywell. Manufacturing company Honeywell used Six Sigma to reduce the cycle time for developing new products by 50%. It helped the company bring new products to market faster than its competitors.
- Motorola. As the birthplace of Six Sigma, Motorola saw a $16 billion savings within a decade of its implementation. It showcased the methodology's potential impact on quality and cost reduction.
Challenges and Limitations of Six Sigma
While Six Sigma offers significant benefits, it has challenges and limitations. Here are a couple of challenges and constraints you need to be aware of
- Resistance to Change and Organizational Culture. Employees and management may be hesitant to embrace new methodologies, especially if they perceive Six Sigma as disruptive or time-consuming.
- Misapplication or Over-reliance on Six Sigma Tools. Organizations may mistakenly believe that using them alone will guarantee success. Focusing solely on tools without a comprehensive understanding of the underlying concepts can lead to suboptimal results.
- Limitations in Certain Industries or Non-Manufacturing Environments. Six Sigma's origins are in manufacturing. It can make its application more challenging in non-manufacturing sectors such as healthcare, education, or government.
Part VI: Six Sigma and Lean Six Sigma – A Comparison
Six Sigma and Lean are two complementary methodologies businesses can use to improve their processes. While they have distinct origins and focuses, they share a common goal: process optimization.
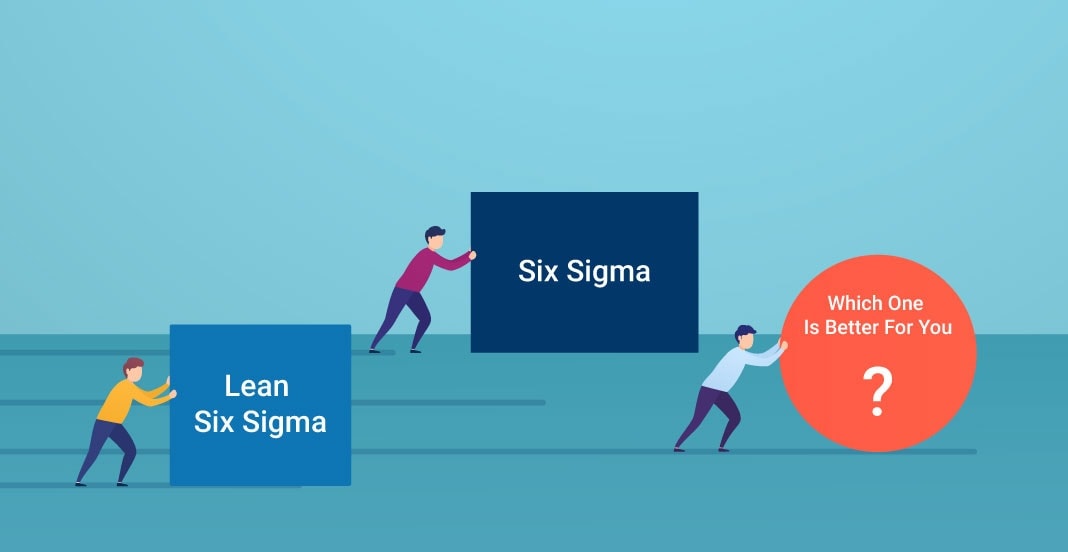
Overview of Lean Six Sigma and Its Benefits
Lean Six Sigma combines the strengths of both methodologies. Here are some examples of how businesses can use Lean Six Sigma.
- A manufacturing company uses Lean Six Sigma to reduce the time it takes to produce a product by 25%.
- A healthcare organization utilizes Lean Six Sigma to reduce the number of patient errors by 50%.
- A financial services company applies Lean Six Sigma to reduce the time it takes to process a loan application by 30%.
Integration of Lean Tools and Techniques With Six Sigma
It is important to note that Lean Six Sigma is not a quick fix. It requires continuous improvement and a willingness to invest in training and resources. Lean Six Sigma practitioners use Lean tools to improve process flow and efficiency. Meanwhile, Six Sigma tools aid in data-driven problem-solving and root cause analysis.
Conclusion
Six Sigma has evolved into various forms. Today, the method includes Lean Six Sigma and Design for Six Sigma, applied across industries. The essence of Six Sigma lies in its dedication to continuous improvement through data-driven decision-making. By analyzing data, businesses can identify and eliminate defects. Implementing it the right way can lead to enhanced efficiency and customer satisfaction.
It's recommended for all organizations to explore and implement their principles. Embracing it can lead to improved processes, reduced costs, and, ultimately, better products and services for customers.